Has Covid-19 presented a threat to or opportunity for supply chain efficiency and productivity? No organisation was prepared for the impact of the crisis, however, those who had already invested in new technologies, going digital and working leaner were better equipped. A Workfront poll of 3,750 employees indicates 56% of staff believe that outdated technology results in declining productivity. Covid-19 has forced many organisations to rethink their strategy when it comes to improving their supply chain and how to best invest in supporting their workforce. In this article, we reflect on ways that new technologies are being implemented across the supply chain to improve business operations.
Factories
Covid-19 has underscored the importance for factories to maintain high health and safety standards for their workers. We have seen companies react to the pandemic by implementing decontamination carpets, mandating temperature checks, enforcing distance between employees, copper fittings (copper has natural antimicrobial properties) and varying levels of personal protective equipment (PPE) requirements. However, extra safety measures have impacted the productivity of employees and have brought other difficulties in terms of communications and ways of working.
Samsung recently deployed an end-to-end 5G solution in their smart ‘digital factory’, resulting in automating over 70% of their manufacturing processes. In turn this has reduced the number of low-skilled employees whilst increasing their need for higher-skilled workers, and consequently a requirement for better training. Samsung also have deployed various connected devices (Internet of Things or IoT) for product quality control, monitoring environmental impacts and maximising productivity on the assembly line. Personal sensors are also used to monitor basic health indicators, such as heart rate and temperature to ensure employees are healthy and fit to work. As factories are traditionally 3rd parties, it will be important more than ever for retailers to work closely with them and understand how best they can support their people during this time. As manufacturing companies ‘regroup', organisations must look to automation and digitisation to ensure the health and safety of their workers, whilst also improving productivity, output and quality.
Delivery and Transport
With packages turning up more frequently at our front doors and labour scarcity due to Covid-19, there has been extra pressure on courier services to become more robust and efficient. However, the demand is not new, with strong, consistent e-commerce growth across the retail sector and expectations for next day delivery as standard. To help them move towards the ‘renew’ phase, data within this space is vital and the use of IoT devices, Artificial Intelligence and Machine Learning can help with the collection of data, analysis and insight.
This need for data-driven insight has been seen at FedEx who have partnered with Microsoft to create services that will drive a higher inventory turn ratio, reduce markdowns and provide their employees with the right level of granular information to make decisions. With fluctuating order patterns, UPS has also invested in technology to improve their Warehouse Execution System (WES) and are also using robotics to meet fulfilment demands and improve productivity. The system monitors the available capacity of employees, fulfilment requirements, backlogs and labour status in real-time to help UPS identify and mitigate against any potential issues. Going forward, delivery and transport providers must continue to invest in building a wealth of data to help track, action decisions and make the end-to end supply chain more visible for their customers. This will provide retailers with the data they need to provide their customers with more accurate times and set realistic expectations. Potential interface integration opportunities with retailers should also be considered as this could improve the customer’s user experience online.
Stores
Many retailers have been able to learn from the grocers and other essential stores on what needs to be in place in terms of hygiene and distancing advice before reopening. As retailers transition to the ‘regroup’ phase however, they should start to think more about how they can reduce the number of employees in their store and increase the number of customers. This could be achieved by automating non-value-add tasks, such as labour scheduling or restocking, and freeing up time for more skilled activities, as seen in American superstore Walmart.
Customers will now need more of a reason to come into stores rather than ordering online. The two can work together in relieving supply chain strains by pushing ‘click and collect’ or using parts of the building as a ‘dark store’ however, it will ultimately come down to the employees to build a differentiated experience. Employees will now need to be more productive and motivated to serve their customers better. Investment into training and upskilling should be a focus for retailers when thinking how best to ‘regroup’ . The review of processes, knowledge in products, expertise and an increase in digital fluency will all be desired in the workforce’s skillset, due to the potential change in the retail landscape.
Opportunity or Threat?
Returning to the initial question posed, we believe that Covid-19 has presented both a threat and an opportunity to organisations. The crisis has forced retailers to reflect on their end-to-end supply chain, to make it leaner whilst better equipping and supporting their employees.
We believe that technology should be implemented appropriately to improve business operations and relieve staff of non-value add tasks. This will help them improve their productivity in the value-add tasks, which may require additional training and upskilling. However, by doing so employees will be able to better support their customers and play a vital role in improving loyalty, which every retailer should always be prioritising.
To learn more about efficiencies and driving improvements within the supply chain, please check our follow-up article within this series - Do you really know your supply chain?
Published
April 29, 2024Reading time
3 minutesRelated posts
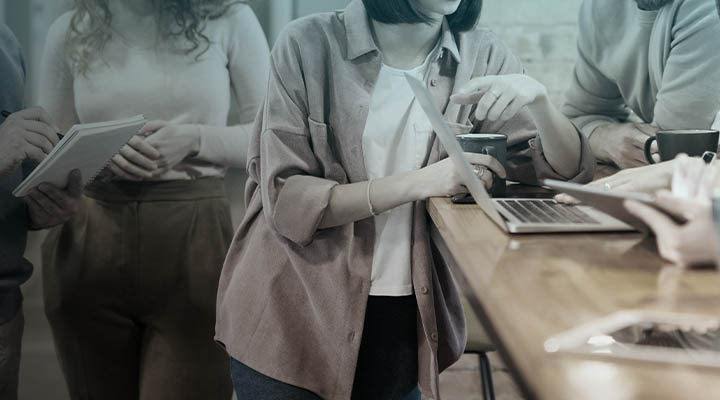